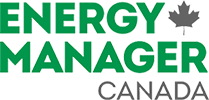
News
Lighting efficiency series: Getting the process right
The importance of replacing existing lighting with more economical fixtures to save energy is especially critical given the current economic climate and the threat of global warming. Over the past year, many companies have seen their revenues fall significantly, affecting their profitability. Energy cost savings from lighting projects can significantly affect the corporate bottom line. If revenues are down, often the only way to profitability is to reduce costs.
October 26, 2009 By Greg Jones
One reason that companies are reluctant to make the change is their thinking that the process is too complex and costly. However a good lighting company can simplify the project and ensure the end result is better lighting and lower operating and maintenance costs. The key steps include:
- Customer Review: The lighting company should discuss the lighting requirements and objectives with the company.
- Lighting Audit: The lighting company should conduct a detailed lighting audit looking at all aspects of the potential project.
- Engineering and Design: The lighting company engineering department will evaluate various options and determine which fixtures are best suited to each individual job. A straight-up one-for-one replacement is rarely the most practical, and it is during this stage that opportunities to reduce the number of fixtures, alter placement, introduce motion sensors and improve light levels, among other things, are possible.
- Lighting Analysis: This step provides the customer with a lighting recommendation which shows how much energy can be reduced, money saved and the resulting lighting effectiveness.
- Government Incentives: The government often provides many incentives to the energy sector to make upgrading a more attractive option, but only after myriad forms are filled out and mailed to the proper people. The lighting company can help manage this process.
- Installation: The key here is to map out the installation process for the customer to ensure minimal workplace disruption. The prospect of saving many thousands of dollars per year by upgrading lighting is appealing, but it becomes less so if it means shutting down production for a few weeks and losing thousands of dollars in production. Sometimes it is necessary to work overnight or weekends to get the work done.
- Incentive Payment and Final Inspection: The final step is not when the installation is fully complete, but when the job is completely finished. This includes the final cleanup, minor adjustments and helping the customer obtain incentive cheques from the government.
When your lighting company is committed to a thorough process, the result is a project that meets everyone’s expectations. A good lighting company will follow every step to ensure a successful project.
Greg Jones (g.jones@nexstarlighting.com) is President of Nexstar Lighting.
Print this page