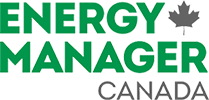
News
Manufacturer saves big following lighting retrofit
Last January 2010, Jacobs and Thompson Inc—a manufacturer of foam and gasket products—decided to perform a complete lighting retrofit of its 89 Kenhar Drive facility, located in Toronto’s west end. The main purpose of the retrofit was to create energy savings, as well as reducing the facility’s carbon footprint.
September 29, 2010 By John Gilson
“The two main reasons for the retrofit were to reduce the plant’s hydro bills, making it more energy efficient, and to reduce the carbon footprint, lowering the amount of greenhouse gases emitted,” said Peter Mauti, Maintenance Supervisor for Jacobs and Thompson, who was responsible for overseeing the lighting retrofit.
Prior to the retrofit, the bulk of the facility’s lighting fixtures were comprised of a variety of T-12 ballasts, as well as 175W and 400W metal halide bay lighting. The facility’s outside lighting was composed of 175W and 400W metal halides. Removing the “inefficient” T-12 fixtures and replacing them with T-8 fixtures would be the primary task for Mauti and his team.
With a total of 242 T-12 fixtures needing to be replaced, this was easier said than done. The existing fluorescent and metal halide fixtures in the low-ceiling height areas of the plant also needed to be replaced—with Bj-Take Inc fixtures model BJT-4LAMP-T8, which according to Mauti provide the highest lumen output. The lower plant areas were to be the first to be changed over, followed by the warehouse where the fluorescent and 400 W high bays were to be replaced with SRS 250 W stingrays.
What made the project particularly difficult were the many challenges it presented to the team. For example, Mauti’s team had to rewire, replace and remove cables throughout the facility that have been in place over many years. “Some of the infrastructure had been in place since the 1950s,” said Mauti.
When everything was finished, the total cost of the replacement and retrofit of lighting fixtures, including some miscellaneous material, was $55,056 plus GST. The price was may have been steep, but it was well worth it. One year after the retrofit, the company estimates the investment will save it $38,641.56 in hydro savings alone. These savings, according to the company, will keep rising as hydro prices continue to escalate.
Mauti attributes much of these savings to the plant’s new fluorescent T-8 bulbs, which offer 20,000 hours of lamp life, considerably higher than the 12,000 hours of the plant’s former T-12 bulbs. In addition, the new metal halide bulbs on the stingrays have a 15,000 hour life, which is higher than the previous 10,000 hours on the regular high bays. Some of the other major benefits include:
· reduced kilowatt consumption resulting in lower hydro bill
· improved lighting level in the plant
· and longer-life bulbs resulting in lower labour costs for replacement
The company expects a complete return on investment (ROI) in approximately 1.5 to 2 years, with local utility and federal government incentives helping to offset some of the installation costs, in particular from BOMA (the Building Owners and Managers Association). In addition to the cost-savings, the company is optimistic about the possibility of reducing greenhouse gas emissions in the near future—after all, being more environmentally-friendly was one of the primary reasons behind the retrofit.
In terms of real numbers, the Jacobs and Thompson plant has already seen a large reduction in energy costs. Previously, the plant’s lighting bill consumed approximately 62,000 kW of energy a month, or $5,695. Currently, with the T-8 fixtures, the plant consumes 25,575 kW a month ($2,475), which is a savings of approximately $3,220.
The whole project was completed in completed in approximately two months. Looking back at the project, Peter Mauti is happy with the results. “The plant has lightened up quite a bit,” he said. “I’m extremely content with the results—I’m very satisfied.”
For more information on the company, go to www.foamparts.ca.
Print this page