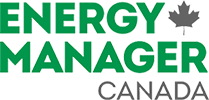
Features
Sustainable Rooftops
An uninterrupted monolithic membrane provides significant energy savings for building owners.
March 4, 2020 By Doug Kramer
It’s no secret that extreme weather linked to climate change is a significant and growing threat. There is also no doubt that facility management stakeholders are having to face the bigger picture and consider the resilience of buildings, enhance operations, better utilize resources and manage energy for cost savings and an overall healthier planet.
Among today’s green building standards and certification systems, we are seeing building management pay much-needed attention to the National Building Code of Canada (NBC) and its guidelines for energy savings and the resilience of roofs. Canadian cities also present some unique challenges for flat roofs due to extreme environmental conditions, both seasonally and diurnally.
For stakeholders in the sprayed polyurethane foam (SPF) and roof coatings industry, these expectations for greener and more energy-efficient products means embracing the bigger picture and offering new blowing agent and roof surface formulations. The new and improved SPFs and roof coating products on the market have a broad range of advantages over their siblings, which includes better RSI or R-Values, airtight building envelopes, added structural support and protection, moisture control and a 40% or more savings in energy costs.
The demand for SPF products is estimated to be approximately 18 to 20% of aggressive growth for the foreseeable future. The market is expected to reach an estimated $2.1 billion by 2023 with a CAGR of 5.4% from 2018 to 2023. Building owners and facility management see the value and are educating themselves on the products’ efficiencies and overall benefits that contribute to a healthier building.
An improved roofing system
The cost of SPF and roof coatings are two-thirds of other flat roof systems because it is also damp proofing and insulating the overall assembly. The coatings must be applied after the SPF is installed. It is an efficient process—SPF sets in seconds, so coating can take place within two hours. The combination of these two protective barriers should be installed during roofing season, which varies based on the location. The foam reacts slowly at sub-zero temperatures—coatings can go down as low as –17C (1 F).
The versatility of spray foam in warm and cold Canadian climate means it is a resilient material that can match the weather extremes forecasted to come. Since spray foam is such an effective insulator, it is being used by the National Aeronautics and Space Administration (NASA) on rockets, tested to both extremely high and low temperatures, to ensure its space-worthiness.
Energy management
SPF seals the building envelope to stop heat transfer through the roof deck, minimizes the escape of conditioned air and restricts unconditioned air from entering the building, thereby saving on costs and energy.
An unsealed or poorly sealed building can leak enough air to fill up to two or more air blimps per day. SPF products are one of the most energy-efficient materials for roofing since it becomes a seamless monolithic membrane once it is applied. With an RSI value of around one per inch (compared to blown fibreglass with an RSI of around 0.35 per inch), spray foam saves on both heating and cooling costs. SPF has a higher RSI compared to polyisocyanurate and expanded polystyrene (EPS), and does not need to be mechanically fastened, thereby decreasing labour time and costs.
Elastomeric protective coatings are next in the process, they are applied over SPF roofs, and most coating products have earned the Cool Roof Ratings Council (CRRC) certification due to its high reflectivity of harmful ultraviolet (UV) rays.
The rating program lends itself to manufacturers and sellers who label their roofing products with measured initial and aged radiative properties. The CRRC currently allows the use of two different thermal emittance test methods for its product rating program: ASTM C1371, Standard Test Method for Determination of Emittance of Materials Near Room Temperature Using Portable Emissometers, and the Slide Method. For SPF, the Slide Method adapts the C1371 instrument for use on specimens with higher thermal resistance, such as concrete or clay tile, wood shingles or insulation-backed membranes. The method involves moving the device head across the sample during the measurement process. Roof coatings come in white, grey, tan and even custom colours upon request.
SPF and coatings are also frequently utilized in Arctic communities where temperatures as low as –32C (–26F) in winter necessitate an airtight building envelope. Whether extreme climates and endorsements like NASA’s are compelling, it is hard to argue with the economics of an SPF roof. Spray foam could also contribute to a ‘cool roof’ effect by not allowing the warm air inside to leak out in the winter and trapping in the cold air in the summer. This could mean energy savings compared to alternative roofing systems. Some coatings, for instance, are 88 per cent reflective and can reduce cooling costs by up to 35%.
A sustainable solution and improved life cycle cost
When it comes to silicone roof coatings that accompany the SPF process, the primerless, single coat application of the product brings efficiency and cost savings to the installation process. Longer durability means lower roof life cycle costs and exceptional longevity.
Spray foam roofs offer a sustainable solution for a wide range of large commercial, agricultural and industrial buildings. Since it can be applied directly on top of existing substrates, it saves time and money that would have been spent on disposal costs and keeps discarded material out of landfills.
Tear-off is not required because, in most circumstances, the substrate does not have to be pulled off to extend the life of the building with proper upkeep. While other roofing systems deteriorate over time and require a complete replacement at the end of their life, spray foam assemblies only require a reapplication of the elastomeric outer membrane every 20 or so years, at a cost of about half the original roof installation. Additionally, repairs are easy to do without having to call in specialized companies. In the unlikely event of the roof getting punctured or cut, maintenance staff can easily make the fix by filling any fissures with polyurethane exterior caulking.
Roofs are usually always considered last when it comes to commercial building maintenance, and they shouldn’t be. They usually get the care they deserve when it’s way too late in the game, when they become frail and start to leak or fail.
Savvy building facility management staff consider roofing an overall asset to their operations, energy efficiency and sustainability goals. Certainly, preventative maintenance and overall life cycle cost is important, but there’s a long-term gain here and that is meeting Canada’s new regulations to eliminate greenhouse gas (GHG) emissions that contribute to global warming, waste reduction and creating a more comfortable building environment for everyone.
Doug Kramer is the president of Icynene-Lapolla, a manufacturer and supplier of sprayed polyurethane foam (SPF) and coatings. He has almost 30 years of experience in the manufacturing, operations, sales, and marketing of a broad variety of elastomeric coatings and polyurethane foam for construction. Kramer is a member of the Center for Polyurethanes Industry’s (CPI’s) Spray Foam Coalition (SFC)and a former board member of the Spray Polyurethane Foam Alliance (SPFA) and. He can be reached at dkramer@icynene-lapolla.com.
Print this page