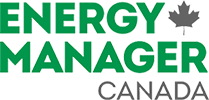
Controls & Automation
Tackling the four Ms of energy management
A maintenance, monitoring, modernization and management plan can give any facility a step up on its competition.
Plant managers today are faced with increasing demands for various performance indicators and equipment health records. In other words, the expectations placed on maintenance managers are growing, due to the increasing sophistication of maintenance technology.
March 17, 2009 By Pratap Reveru
Consider the changing approach as a generational development:
- The first generation expectations were: Fix equipment when it’s broken.
- Second generation: Time-based maintenance to achieve higher plant availability.
- Third generation: A mix of preventive and predictive maintenance to achieve greater safety and higher plant availability (minimize equipment downtime).
- Fourth generation: Reliability-centered maintenance to maximize employee and equipment safety — operating equipment efficiency (OEE).
For example, consider electrical substation management. In North America and Europe, most electrical substation equipment is reaching the end of its useful life. These substations were designed and commissioned with available standards, specifications and the technology available at that time.
Consider that 30 to 40 years ago circuit breakers were air and oil-based. Protective and control schemes used discrete devices for protection, metering and control. Eletromechanical relays performed protective functions; instrumentation provided the only metering; auxiliary relays and human interaction were responsible for maintaining substation control.
Modern research and development has made it possible to increase the efficiency and benefits of electrical distribution equipment. Today we have more advanced technology, such as Vacuum or SF6 breakers, multifunction protective relays and arc resistant switchgear. When equipment is commissioned, only one line diagram is posted in the control room to facilitate future operation and maintenance of the equipment.
But a maintenance and modernization plan is the key to achieve reliable, long-term equipment operation in any facility. So plant managers should give top priority to preparing a master equipment maintenance plan similar in scope to the one line diagram. Older plants also require a modernization plan, to pinpoint which equipment needs upgrading, and new standards that need to be implemented. Such a plan improves the plant’s bottom line.
Expanding the maintenance perspective
Today’s equipment is loaded with features that enable plant engineers to easily gather diagnostics. Experience has shown that by using the latest technology to modernize existing equipment, performance is improved and useful life is extended. For instance, traditionally, in most electrical substations, electrical distribution assets are maintained in one of two modes. The first mode is “fix it when it breaks”; the second mode is “time-based maintenance.” Many industrial facilities operate in the same manner.
A better way to maintain equipment is a maintenance, monitoring, modernization, and management plan (MP4). An MP4 helps plant managers by evaluating the current performance of the equipment and measuring actual against required business performance levels. It also determines the causes of deterioration and recommends ways to improve performance.
This MP4 identifies possible modifications, evaluates equipment modernization and operation and maintenance techniques. Using this approach, failure becomes defined as the point at which equipment fails to perform according to its intended function, rather than simply determining whether the equipment is working or broken down.
Today, maintenance procedures should be included in asset maintenance programs. This includes condition-based tasks to check for potential failure, such as visual inspection or predictive technologies such as breaker operation analysis, temperature monitoring and other methods. New services application software such as “IBsuite” can help in this analysis.
MP4 architecture
An MP4 system involves collecting a wide variety of electrical distribution equipment data during an on-site inspection, such as history of maintenance records and diagnostics, and then processing the data to identify equipment health. Collected data can be analyzed by a consultant to understand the strengths and weaknesses of the installation and equipment; major risks according to process/business needs; and solutions to manage the risks and optimize performance. Priorities are clearly identified within a framework based on four plans:
- Maintenance plan: Keep the installation running.
- Modernization plan: Manage equipment obsolescence and performance improvement.
- Monitoring plan: Monitor risk in terms of availability, power quality and energy costs.
- Management plan: Ensure the safety of people and optimization of costs.
The program architecture and functions make it the best approach for evaluating electrical distribution asset performance. An effective system must include:
- A stress level analysis, to determine operational conditions, environment and aging;
- A reliability analysis, to determine the critical equipment within the architecture;
- A criticality index, analyzing the health of electrical assets by combining reliability and stress to compute for equipments; and
- Solutions to manage the risks and to optimize performances and financial risk evaluation.
An MP4 consultative process assesses the performance of electrical installations and provides recommendations for improvements to meet a business’s energy needs.
The methodology
The MP4 methodology, as used by Schneider Electric consultants, is based on four steps:
STEP 1: Specification of electrical energy needs. The electrical energy requirements of a business are specified following a process analysis. A model plant operation is created using information gathered in this process. This will identify the critical process points from the electrical energy supply point of view, and also characterize unwanted events that need to be prevented such as: blackouts, voltage dips, harmonics, etc. It will also pinpoint the devices or busbars on the installation’s single line diagram that are able to trigger the high-risk unwanted events. The process helps to establish the main energy consumption points and defines their load. The costs of the unwanted events (production downtime, machine start-up costs, production, quality problems, etc.) are evaluated based on the data gathered within the facility. This cost analysis helps to clarify the economic advantages of the conclusions and justify recommended actions to senior executives – a critical requirement for any facility manager.
STEP 2: Assessment of stress level to which the electrical equipment is subjected. The second step consists of identifying the key devices with respect to the required performance. For each piece of equipment, a stress indicator quantifies both the environmental characteristics and the operating conditions. In addition to this, a qualitative assessment of the equipment state should be performed by an equipment consultant and backed up by software analysis.
STEP 3: Electrical network performance analysis. A reliability analysis quantifies the level of risk in relation to the network architecture and its operating modes. This analysis determines the contribution of each device/equipment to the unwanted events probability. The first step of a reliability study is positioning the unexpected events. “Unexpected Event” (UE) is a typical terminology used in the reliability domain, to identify the critical failure that will lead to catastrophic damages (human, financial, ecological…). In the application to electrical networks domain, one UE refers to one busbar: the UE represent the interruption of power supply to this busbar. Therefore, we define as UEs only those busbars which are really vital for the facility.
STEP 4: Solutions to manage the risks. Combining the stress level with the reliability calculation results in a criticality index and a corresponding service policy defined for each device. The criticality index can be calculated using available software that runs a reliability algorithm. The criticality calculation gives for each electrical device, an index that represents and resumes its level of criticality to ensure the correct functioning of the electrical network and the continuous power supply of essential loads. An MP4 report focuses on the organizational aspects of operating and maintenance activities. It also backs up and completes the technical recommendations implemented through the maintenance, monitoring and modernization plans, giving an economic control over these technical recommendations.
Investment guide
To improve the performance level of the electrical power supply system, and to reach a higher value of its availability, it will be necessary to modify the architecture of the electrical network, and to reduce the repair time of electrical devices through a spare parts policy to meet energy needs. Modernization and management plans can have an effective impact on power supply availability.
The MP4 approach aims to create a reliability-centered maintenance plan that matches the maintenance to be carried out based on the device criticality index, while the retrofit schedule aims to optimize the reliability of critical devices. A customized maintenance plan ensures that the expenditure on maintenance is optimal, and that the most critical devices receive the most suitable maintenance, to keep functioning correctly. At the same time, it will reduce corrective maintenance costs by preventing device failures and reducing the failure rates of electrical devices. Furthermore, implementing a monitoring system creates an opportunity to survey energy consumption and identify opportunities for energy savings.
Conclusion
The MP4 consultative program is designed to assist plant and maintenance managers by evaluating the current performance of their equipment and measuring this actual against required business performance levels. It further proceeds to determine the causes of deterioration, equipment reliability and recommends ways to improve performance. Recommendations may include possible modifications, equipment modernization methods and operation and maintenance techniques.
The objective of this consultative program is to develop and propose a plan that strikes an optimal balance between investment and cost savings. Other key benefits realized by the MP4 process include: decreased breakdown costs resulting from reduced number of breakdowns and downtime, optimized energy savings resulting from increased electrical network performance and increased safety.
Pratap Revuru, P.Eng., is Manager, Power Systems Engineering at Schneider Canada Services & Projects. He can be contacted at pratap.revuru@ca.schneider-electric.com.
Print this page