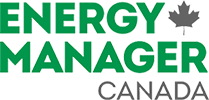
HVAC & Plumbing
Variable-flow refrigerant systems: Ground source heat pumps without the ground?
When designing the mechanical system for our new headquarters at A Grander View, Enermodal Engineering chose to use a variable-flow refrigerant (VFR) multi-split system. Although this system is not new—it is frequently used in Japan—it is a relatively unusual system in Canada, as suppliers only recently developed units that can operate reliably throughout our winters. The VFR system has proven highly effective. Our office building is considered the most energy-efficient office in Canada, using 75 kWh/m2 (the Canadian average is 375 kWh/m2).
July 7, 2010 By Stephen Carpenter P.Eng
What kind of system is it?
Typical small- and mid-size office buildings are heated by gas-fired roof-top units or boilers and cooled by rooftop DX type air conditioning units. Conventional DX (or direct expansion) systems have one evaporator for each condenser and operate either full-on or full-off, cycling as required to meet actual space needs.
VRF systems have multiple indoor units connected to an outdoor unit. At A Grander View there are three outdoor rooftop units, each connected to 20 indoor units (there are 20 units per floor). There is no water piping and minimal ducting in this system. Refrigerant piping strings all the evaporators together in series and is used to transfer heat and coolth to the space rather than moving air or water. (This system requires a separate ventilation system.)
The system is called variable-flow since a varying amount of refrigerant is circulated depending on how many units are calling for heating or cooling—this enables customized thermal conditions for different spaces and heat recovery between zones.
At A Grander View, the entire system is controlled by occupancy sensors that send a wireless infrared signal to the automation system integrated into the fan coils. This sophisticated automation system allows the building engineers to control the system operation, including on/off, heat/cool and fan compressor speeds. There is no building operator.
Benefits to the VRF system
Energy Efficiency
Typical heating/cooling systems have energy losses in the duct system. Additionally, most HVAC systems operate at 40-80% capacity during operating hours resulting in frequent cycling of equipment, whereas the condensers in a VRF system operate at variable speeds, enabling high part-load efficiency and better dehumidification.
By operating at varying speeds, the COP (ratio of heat out to electricity in) is much higher than conventional air-source heat pumps. The seasonal COP for a building in southern Ontario with VRFs is approximately 2.6; not far below the seasonal COP values that are seen in ground source heat pumps. A VRF system was used at A Grander View to help achieve an 82% energy reduction over a conventional building.
Individualized Comfort
Each zone has its own evaporator with customized setpoint control. Because VRF systems have variable speed compressors with wide capacity modulation abilities, the delivered temperature is very precise (within 0.6oC). VFR systems work best in buildings that require individualized control of spaces, such as office buildings, and multi-unit residential buildings. This technology is not particularly suited to large buildings where economics and performance favour large central systems or warehouses or big box stores where good zone control is not required.
Simpler Installation
In typical HVAC systems, a chiller is installed with a crane. VRF systems are lightweight and do not require large installation equipment. They are compact and fit in an elevator. The installation can also be staged, floor-by-floor, to accommodate tenanted spaces where only part of a building is occupied.
A VRF system is a great option for a retrofit of a historic building as smaller ductwork (only needed for the ventilation system) is added and the basic structure of the building can remain unaltered.
Since the heat pumps operate using electricity, no natural gas service to the building is necessary.
The Cost
Although the incremental cost of a VRF system over a rooftop VAV system is highly variable, most sources cite 5-20% increased construction costs.
At A Grander View the cost of the total mechanical system was $40/sf, only slightly more than a conventional building. The VRF equipment was more expensive than a rooftop system but considerable savings were realized by reducing or eliminating ductwork, VAV controls and natural gas piping in the building.
Stephen Carpenter is president of Enermodal Engineering, the largest green building consulting firm in Canada. Operating since 1980, Enermodal has offices in Kitchener, Calgary, Edmonton, Denver, and Toronto. Enermodal has certified 40% of all LEED Canada certified buildings.
Print this page